
Drying up inefficiencies in manufacturing processes
UMN project aims to make paper manufacturing more efficient – and that’s just the beginning.
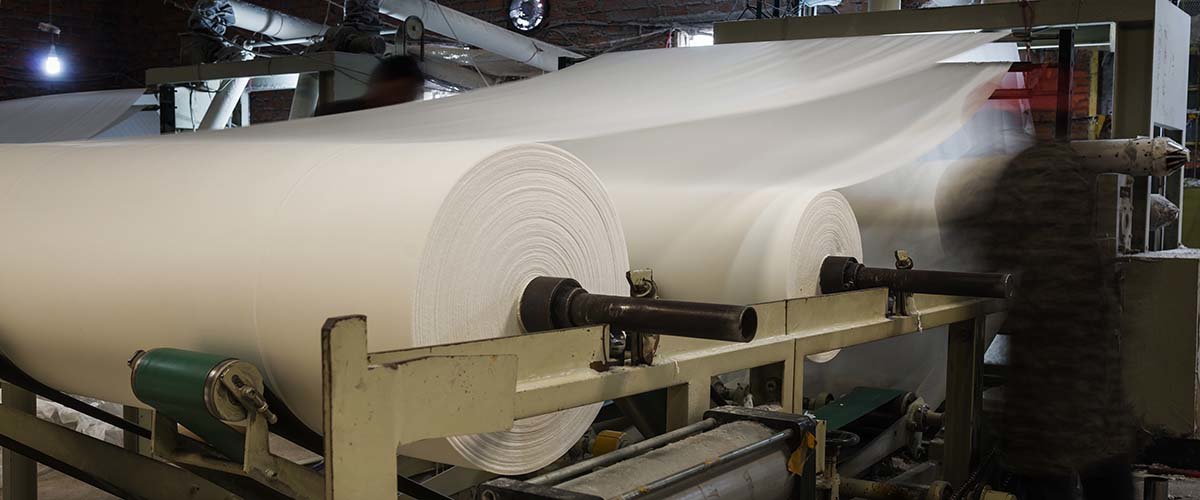
Shri Ramaswamy, PhD, wants to do for manufacturing processes what microwave ovens did for meal prep: improve speed and efficiency. Only instead of heating food, he’s drying paper, board and other products.
His team in the Department of Bioproducts and Biosystems Engineering at the University of Minnesota is working to make energy-intensive manufacturing processes more efficient, starting with pulp and paper production. By substituting fossil-based energy with renewable energy, they aim to decrease the carbon footprint of manufacturing processes.
Paper is a biomaterial, which means it readily interacts with water and the water is difficult to remove, requiring a significant amount of energy. The manufacturing process begins with a slurry of natural fibers that is diluted into pulp, then mechanically dewatered and pressed. That material is then dried and made into finished paper products. Conventional drying methods use slow, inefficient technologies and often, fossil-based energy.
Funded by a three-year, $3 million grant from the United States Department of Energy, Ramaswamy and his team are developing a hybrid drying approach that incorporates auxiliary energy inputs such as electromagnetic energy and acoustic energy into the conventional drying process. The goal is to improve energy efficiency as well as the environmental sustainability of conventional drying processes.
“We believe there is an opportunity to combine these energy sources to remove water more quickly and dry the paper more efficiently,” said Ramaswamy, who has educational background in chemical engineering and paper science and engineering, and who spent nine years working in the pulp and paper industry. He likened it to heating food in a microwave oven instead of a traditional oven.
“Microwaves use volumetric heating to heat the entire volume of a food, so it takes less time than cooking in the oven,” he said. “This is an example of a process that circumvents the problem of conventional heating from the outside in. Similarly, we need to find intensified process solutions for pulp and paper manufacturing. If we decrease the total amount of energy and fossil-based energy needed in the process, then we also decrease costs and reduce carbon intensity.”
Industry support
Project collaborators include Savannah River National Lab, RAPID Process Intensification and Deployment Institute and Electric Power Research Institute. It has broad support from the pulp and paper industry including the Alliance for Pulp and Paper Technology Innovation (APPTI), manufacturing companies and their supplier partners. Minnesota-based Liberty Paper, Inc., a large, integrated 100% recycled paper and board manufacturer, is one of the companies supporting the project.
“We are committed to finding ways to improve water removal and drying efficiency during paper manufacturing,” said Thomas Murphy, technical manager at Liberty Paper. “The applications used in this project will help decrease overall energy consumption, lower operating costs and reduce the bottlenecks within the water removal process.”
According to the APPTI, the industry has set a goal to achieve a 50% reduction in greenhouse gas emissions by 2030, against a 2005 baseline.
“The pulp and paper industry is a leader in manufacturing sustainability because we produce easily recyclable products from renewable resources,” said APPTI Executive Director David Turpin. “A major portion of the energy used in producing paper products is consumed in the paper drying process. This project has the potential to significantly reduce energy use and thereby reduce greenhouse gas emissions, helping the industry reach our greenhouse gas reduction goal.”
Broader applications
The Department of Bioproducts and Biosystems Engineering is jointly affiliated with the College of Food, Agricultural and Natural Resource Sciences and the College of Science and Engineering at UMN. Its mission is to integrate engineering, science, technology, and management for the sustainable use of renewable resources and the enhancement of the environment.
This project is a prime opportunity for students to gain hands-on experience in the lab. It kicked off in August, and the team is already exploring innovative drying experiments. What excites them most is that if this works, it could be applied to any material that requires moisture removal in the manufacturing process.
“This project has broad implications well beyond pulp and paper,” said Ramaswamy. “It has the potential to help improve the economic viability and environmental sustainability of the U.S. manufacturing sector.”